EDM
Ultra-Brass wire
The Ultra-Brass EDM wire is a high-quality electrode manufactured by the Dutch company Novotec, available exclusively through an authorised dealer network. Over 30 years of experience in the production of EDM cutting wires have resulted in the development of fully automated machines for the production of electrodes of the highest quality and stable operating parameters. Production is continuously monitored by Novotec's engineering team.
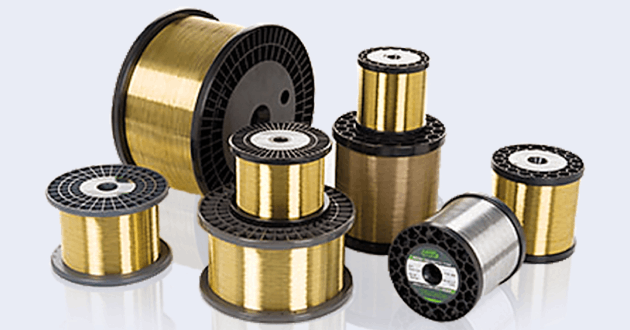
- Manufactured from pure copper and zinc.
- Reliable during automatic threading
- Excellent surface quality
- High cutting speed
- Stable machining free from electrical shorts
- Geometric precision
- Paraffin-free
- Oxidation protected packaging
Drawing | Spool type | d1 | d2 | d3 | d4 | d5 | d6 | e1 | l1 | l2 | Material |
![]() | K125 | 125 | 80 | 16 | 24 | 7 | 3 | 20 | 125 | 100 | PS black |
K160 | 160 | 100 | 22 | 34 | 13 | 3 | 32 | 160 | 128 | PS black | |
K200 | 200 | 125 | 22 | 34 | 13 | 3 | 32 | 200 | 160 | PS black | |
K335 | 335 | 224 | 36 | 60 | 26 | 5 | 80 | 200 | 160 | ABS black |
Drawing | Spool type | d1 | d2 | d3 | d5 | e1 | l1 | l2 | Material |
![]() | P5 | 160 | 90 | 20 | 5 | 25 | 114 | 90 | PS grey |
P10 | 200 | 90 | 30 | 12 | 30 | 134 | 110 | PS grey | |
P15 | 250 | 110 | 34 | 15 | 34 | 140 | 110 | ABS black |
Wire diameter (mm) | Composition | Diameter tolerance (mm) | Tensile strength (N/mm²) | Elongation (%) | Conductivity (%IACS) |
0,20; 0,25; 0,30 | semi-hard Cu/Zn=65/35 | ± 0,001 | 500 (72500) | > 15% | min. 25 |
0,15; 0,20; 0,25; 0,30 | hard | ± 0,001 | 900 (130500) | < 3% | min. 22 |
Wear parts
EDM cutting is a very precise and demanding process that Novotec has been engaged in for more than 25 years. All products used in EDM require high quality, so Novotec designs and manufactures most of the wear parts in-house. The products have a unique symbol for identification and cataloguing.
The wear parts we supply are 100% comparable to original parts from machine manufacturers. We use identical materials which means that there are no differences in quality, shape and dimensions, as well as in installation and operation. Production of wear parts is supervised by well-trained engineers with access to the latest advanced technologies. Each product undergoes extensive quality control after which it is protected by NOVOTEC's proprietary packaging. Each package is tailored to the product and assures the quality and authenticity of NOVOTEC. We conduct continuous monitoring regarding changes introduced by machine manufacturers, which allows us to quickly modify wear parts.
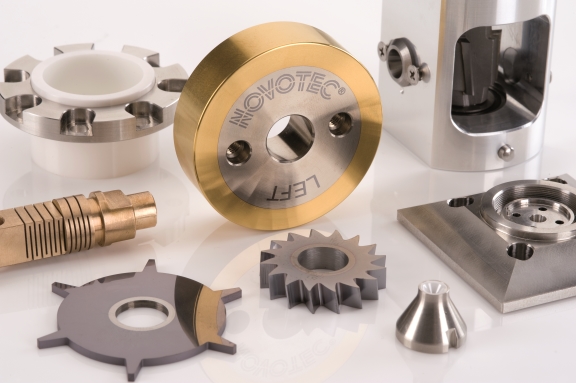
Ultra-Clean filters
Due to faster processing, modern hollowing machines produce more waste, as a result of which the filter has to absorb much more impurities. Taking into account these requirements, Novotec has developed the ULTRA-CLEAN filter equipped with polyester mesh as a filtering material, much better than the traditionally used paper. The polyester mesh is characterized by a dense and uniform structure, and allows filtration of less than 1 µm, which is essential for effective processing. It is much thinner than paper and has much higher mechanical stability. The combination of thinner material and a patented assembly technique means that a filter of the same size can neutralise up to 50% more waste.
ULTRA-CLEAN filters have up to 3 times the service life of conventional paper filters. They also have high corrosion resistance thanks to their protected surface. They are unquestionably the best possible choice for modern wire rodding machines - no other filter combines such high quality filtration and low operating costs.
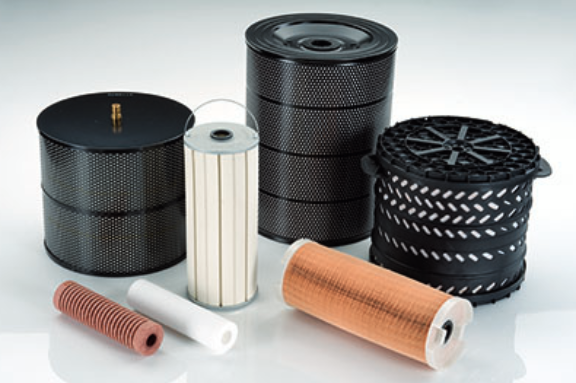
Benefits of using ULTRA-CLEAN filters:
- very fine filtration level
- increased durability of the resin
- less secondary discharge and wire damage
- increased durability of valves and other mechanical components
- increased reliability of the automatic wire threading system
- reduced corrosion of the machine
- longer filter life
Deionisation
When cutting with a wire electrode, water is used as an electrical insulator to avoid premature discharges. A prerequisite for efficient processing is the accurate determination of the insulator's resistance. At the same time, impurities and chemical changes created during the hollowing process cause a constant increase in the conductivity of the water, so constant deionisation is necessary. Any change in resistance is monitored by a sensor, as a result of which the controller activates the water deionising mechanism.
Deionising resin
Specially developed for EDM due to its electrical insulation requirements. We stock a high-quality resin for EDM, guaranteeing optimal operation and the shortest process cycle. It is characterised by maximum service life, finding application in all types of machining. It is available in 25-litre plastic bags or in 50-litre plastic drums to ensure complete tightness during storage.
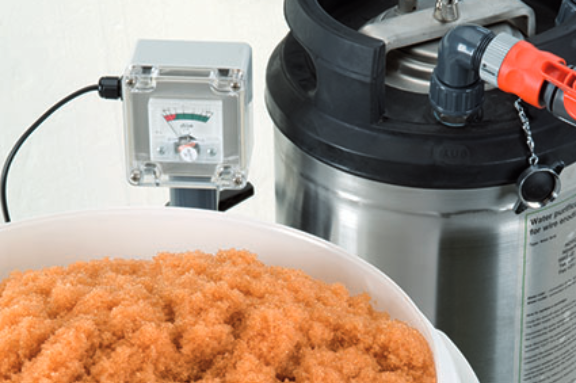
Tubes
Tubes are designed for use on sinker EDM and EDM drilling machines. They are available in two versions with a single hole, used for through-holes drilling, and multi-channel (webbed) designed for blind and through-holes drilling. A single-hole tube acts like a pipe drill, leaving a core of the material inside, which can make flushing difficult. Multi-channel electrodes rotate during the hollowing process, leaving no core, making it possible to drill blind holes and increasing efficiency when hollowing through holes.
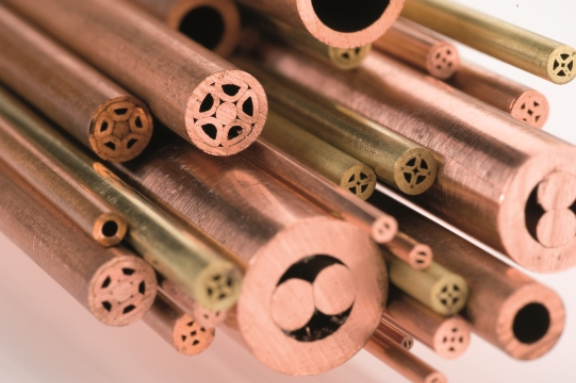
Characteristics:
- material: copper, brass, graphite, tungsten carbide
- single or multi-channel
- used in sinker EDM and EDM drilling machines
- diameters from 0.10 mm to 20 mm
- lengths from 150 mm to 400 mm
Graphite
The two main materials used for EDM are copper and graphite. Initially, only copper was used, but for more than 20 years, it has been known that due to its speed, graphite is more economically viable. The only disadvantage of graphite is the dust that is raised during processing. Graphite is superior to copper in most technical aspects. It is characterised by several times faster processing and, consequently, significantly reduces production costs. Even complex electrodes can be produced faster, more easily and without burrs. Large, heavy copper electrodes reduce machine accuracy. The specific gravity of graphite is 80% less than copper! Large- and medium-grain graphite has a higher rate of metal removal, while when a finely finished surface with low roughness is needed, we use fine-grain graphite.
Advantages of graphite:
- no changes due to temperature
- no warping during electrical discharges
- low expansion coefficient (1/6 that of copper)
- is completely free of internal stresses
- no warping and bending during electrode manufacturing and processing
- dimensional stability
- minimum section or wall thickness from 0.30 mm
- better material removal
- high wear resistance
- possibility of selecting the optimum grade for the application
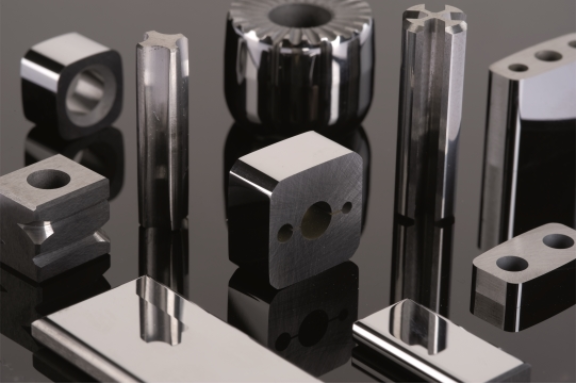