Punches and dies
The punches and dies produced by MX NORM impress with their reliability and accuracy, which is the result of many years of experience in the production of high-precision components for tools, moulds and stamping dies. Examining the material structure and regular inspection of raw materials, computer-controlled vacuum hardening, examining the structure after hardening, numerically controlled CNC machines and state-of-the-art measurement systems during the production and during the final inspection are the basis for creating high-quality products. The wide range of applications of standard and special punches, dies, and stamping die components is confirmed by, among others, customers operating in the automotive, electronics, and household appliances sectors.
What makes us stand out:
| ![]() |
Specialised machinery and experienced workers
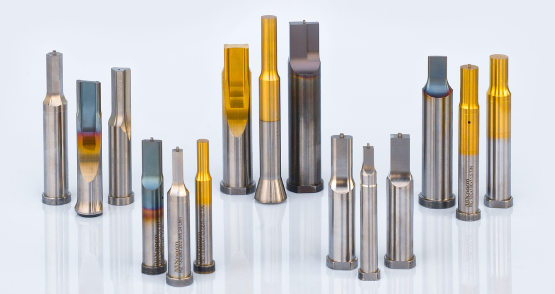
Punches
- with cylindrical head ISO 8020 A, B, C
- with cylindrical head, tuff punch
- with countersunk head DIN 9861 D, DA, C, CA
- with bottle-neck head D, DA
- with cylindrical head and ejector pin ISO 8020 E, F i G
- with countersunk head 30°
- special versions
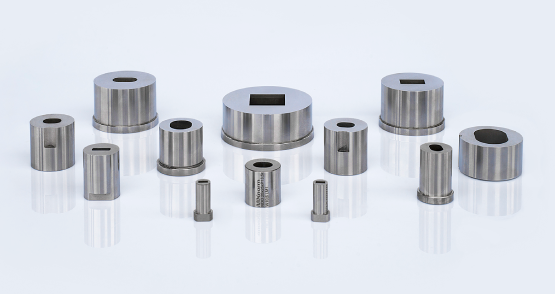
Die buttons
- with flange ISO 8977 B
- without flange ISO 8977 A
- heavy loads with flange
- heavy loads without flange
- Ball-Lock type
- special versions
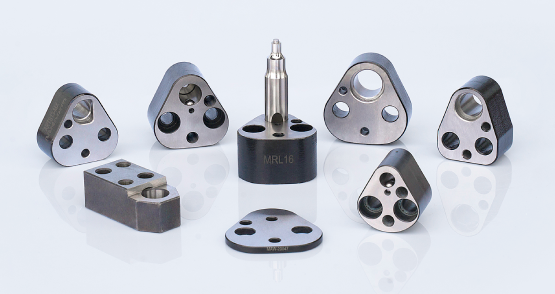
Retainers
- for cylindrical head punches ISO 8020
- for heavy-duty cylindrical head punches
- for Ball-Lock punches
- for bottle-neck punches
Excellent suppliers of semi-finished products and coatings
Materials
By using appropriately selected materials, we can be sure that we produce tools best suited to the customer's needs
- high speed steel HSS ~ 1.3343 ~ SW7M ~ M2
- cold work steel HWS - 1.2379 ~ NC11LV ~ D2
- powder steel CPM 10V
- powder steel Vanadis 23
- tungsten carbide
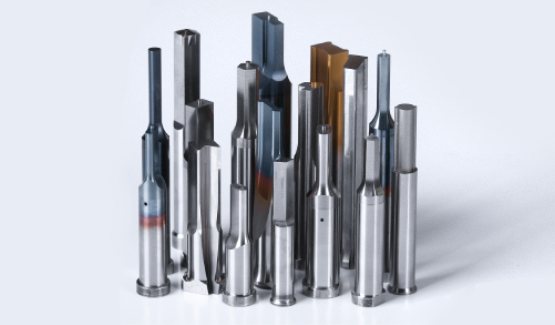
Strict quality control at every stage of production
Coatings
We recommend using coatings on cutting parts operating under heavy loads, at high speeds and in large-scale production. The use of an appropriate coating allows you to significantly increase the tool's operating parameters, directly affecting:
- quality of punching surface
- extending the tool's service life several times
- increase in productivity
- reduction of downtime
- reduction of scrap sticking
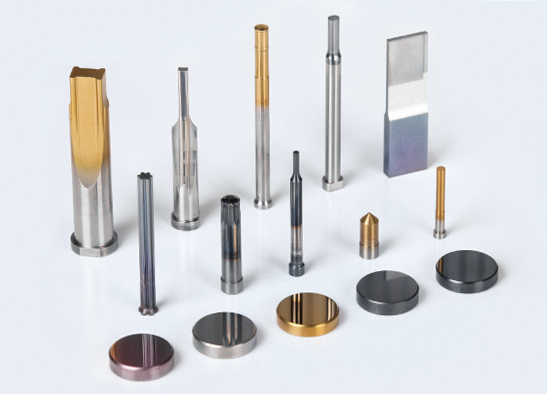
We apply coatings in cooperation with Voestalpine.
Choose the right coating for your tool:
- TiN – titanium nitride
- TiCN – titanium carbide
- CrN – chromium nitride
- ZrN – zirconium nitride
- TiAlCN – Variantic®
- AlCrTiN – Tigral®
- TiAlN – Topmatic®
- AlCrN – Crosal® Plus
- AlTiCN – Exxtral® Plus
- DLC - Sucaslide® and Carbon-X®
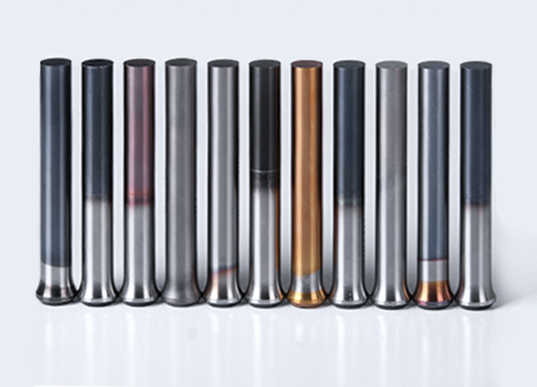
MX NORM punches and dies catalog
Choose the right product and check the technical parameters in the catalog.
Download MX NORM punches and dies catalog |
Online store
Check the availability and prices of punches and dies in our online store.
Go to the B2B store |